Despite Pandemic, Life Science and Biomanufacturing Continue Growth in Greater Boston
September 14, 2020 - By Contributed by Garrett Larivee and Chris Chou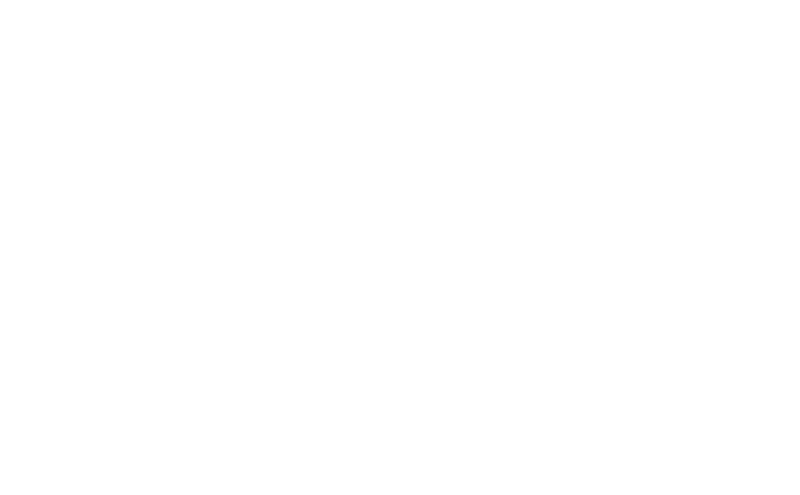
BOSTON–At a time when many hotels and retail businesses are struggling to survive, and the office market remains uncertain as companies ponder the right mix of traditional use with WFH strategies, the life science and industrial sectors continue to be the shining lights among commercial real estate. In the Greater Boston region – generally recognized as the biotechnology capital of the world – life science in particular continues to thrive. Cambridge vacancy rates hover just above zero, asking rents remain near peak levels and demand continues to fuel development pipelines – with much of the space now under construction already pre-leased.
In fact, the pandemic seems to have had little effect, and may have actually spurred further development activity. In July, a joint venture of life science giant Alexandria Real Estate Equities and National Development purchased the 6.6 acre Mt. Auburn Club in Watertown for conversion to a new laboratory/office development; BioMed Realty will soon close on the XMBLY Campus of Assembly Square in Somerville (162,000 square foot office building plus 7.5 acres of adjacent land for future development); and Related Beal and Alexandria are actively pitching large-scale projects in the Seaport. Related submitted a proposal for a one million square foot life science/office/residential project at the 6.5 acre former Gillette World Shaving Headquarters site in July, and Alexandria is hoping to build a life science tower at what was supposed to be the new GE headquarters on Necco Street. In addition, Manulife is marketing 130,000 square feet of its former headquarters at 601 Congress in the Seaport as “lab ready” shell space, reflecting an office-to-lab conversion trend that continues to gain traction.
And why not? Spec lab development continues to pay dividends, as evidenced by the recent lease of 263,500 square feet by Cambridge biotech firm CRISPR Therapeutics at 105 West First Street in South Boston. The lease was signed just four months after Tishman Speyer’s life science development entity Breakthrough Properties broke ground on the site. On the heels of that deal, Bristol-Myers Squibb Co. announced they will be taking 360,000 square feet of build-to-suit at Cambridge Crossing.
Life science deals for lab, office and R&D facilities have garnered the lion’s share of headlines in recent months, but there has also been a quiet surge in demand for the development of biomanufacturing facilities in the region as well. “It’s something that we’re extremely focused on right now,” said Rob Albro, managing director at King Street Properties, the largest private developer of life science properties in the region, at a webinar hosted by ULI Boston in May. “We have a number of biomanufacturing tenants in our portfolio, and it’s a growing area. In our minds, it’s the next level of life science.”
While some of the increased demand for biomanufacturing facilities has been driven by the vulnerabilities of the supply chain exposed by the pandemic, it also has to do with the changes going on within the science of drug manufacturing, according to Albro. More specifically, there has been a shift from small-molecule drugs associated with traditional pharmaceuticals to large molecule drugs (also known as biologics, such as Humira and Remicade) – which require more sophisticated manufacturing processes.
With this new process, the scientist doing the research needs to be more directly involved in the drug production itself, which means they need to be within close proximity to the biomanufacturing facility. But with asking rents in Kendall Square topping $100 per square foot and developable land prices in the Cambridge/Boston/Inner Suburban research hubs continuing to skyrocket, developers are turning to markets beyond Route 128 to construct biomanufacturing plants – generally within an hour’s drive.
“There are big opportunities beyond the state’s biotech core, which are becoming increasingly popular among companies that are looking to save money, while retaining quality and access,” said Meredith Harris, executive director of the Marlborough Economic Development Corporation in the recent MassBio report. “The 495/MetroWest Corridor, a cluster of 22 communities west of Boston, offers an existing ecosystem of big and small biotech players that is similar to the one found in Boston and Cambridge, but that allows them to pay up to three times less for the same quality of commercial property.”
In late 2019, King Street completed the conversion a 100,000 square foot former newspaper printing facility in Framingham into a Class A bio-manufacturing space and R&D laboratory – that is now 100 percent occupied. The developer recently entered into a partnership with a Boston-based investment firm to build biomanufacturing facilities in the Greater Boston market, and acquired land in the Devens Industrial Park (located approximately 35 miles from Boston), citing Devens’ lower cost, supportive local government, and existing life science base as factors in the decision to pursue development at the park.
They are not alone in pursuing this emerging product type. Newly formed Galaxy Life Sciences recently signed a land deal with the Worcester Business Development Corporation (WBDC) to build a $50 million biomanufacturing facility at The Reactory, a 46-acre master-planned campus at the site of the former Worcester State Hospital. The deal also grants Galaxy Life Sciences the right to develop the remainder of the available lots in the biomanufacturing park, which provides up to 470,000 square feet of development with eight parcels ready for development.
The WBDC had previously inked a deal at The Reactory with Chinese biomanufacturing company WuXi Biologics, which will construct a $60 million, 107,000-square-foot, two-story facility – its first-ever manufacturing site in the United States – that is expected to be operational in 2022. In addition, Thermo Fisher Scientific Inc. plans to build their own $180-million, 290,000-square-foot biomanufacturing site in Plainville, MA, also expected to be completed in 2022.
Going forward, the trend should continue to accelerate. A recent report by Mass Bio, “State of Possible 2025” – which lays out the challenges that Massachusetts faces in order to retain its ranking as the world’s top life science hub – indicates that more than $1.9 billion has been invested in new or expanded biomanufacturing facilities by companies in the last five years. However, the report goes on to point out that “despite this success, there is a perception that Massachusetts still lacks capabilities on the manufacturing side…Yet, the opportunity exists to further expand manufacturing capabilities in Massachusetts.”
One of the great strengths of Greater Boston commercial real estate has been its ability to respond to the changes in the market. Life science development and re-development will only continue to grow, and biomanufacturing appears to be the next frontier in life science. If the office to lab conversions continue to trend, we can expect to see a trickle-down effect on the office market. Office buildings should benefit as the impact from subleases and upcoming downsizing of corporate offices will be somewhat offset by these conversions.
Garrett Larivee is Executive Vice President and Chris Chou, Vice President of McCall & Almy - a privately owned brokerage services firm in downtown Boston.
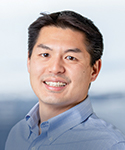
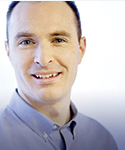
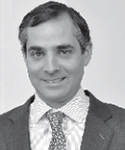
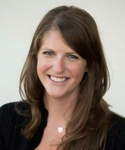